The Role of Algorithms in Supply Chain Management: Enhancing Efficiency and Decision-Making
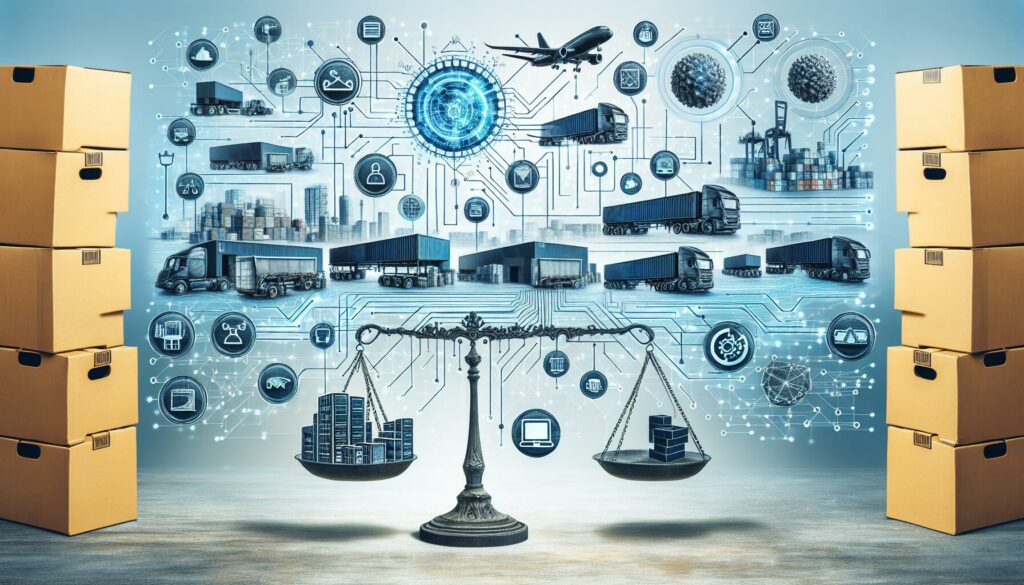
In today’s rapidly evolving business landscape, supply chain management has become increasingly complex and data-driven. As companies strive to optimize their operations, reduce costs, and improve customer satisfaction, the role of algorithms in supply chain management has become more critical than ever. This article explores how algorithms are revolutionizing supply chain processes, from demand forecasting to inventory management and logistics optimization.
Understanding Algorithms in Supply Chain Management
Before delving into the specific applications of algorithms in supply chain management, it’s essential to understand what algorithms are and how they relate to this field. An algorithm is a step-by-step procedure or formula for solving a problem or accomplishing a task. In the context of supply chain management, algorithms are used to process vast amounts of data, make predictions, and optimize various aspects of the supply chain.
These algorithms often leverage techniques from fields such as operations research, machine learning, and artificial intelligence to tackle complex supply chain challenges. By harnessing the power of algorithms, supply chain managers can make more informed decisions, improve efficiency, and gain a competitive edge in the market.
Key Areas Where Algorithms are Transforming Supply Chain Management
1. Demand Forecasting
Accurate demand forecasting is crucial for effective supply chain management. Algorithms play a significant role in improving the accuracy of demand predictions by analyzing historical data, market trends, and external factors. Some common algorithmic approaches used in demand forecasting include:
- Time series analysis
- Machine learning models (e.g., Random Forests, Neural Networks)
- Bayesian inference
- Ensemble methods
These algorithms can process large volumes of data and identify complex patterns that human analysts might miss. By providing more accurate demand forecasts, companies can optimize their inventory levels, reduce stockouts, and minimize excess inventory.
2. Inventory Management
Effective inventory management is a balancing act between having enough stock to meet customer demand and avoiding excessive carrying costs. Algorithms help in this area by:
- Optimizing safety stock levels
- Determining reorder points
- Calculating economic order quantities
- Identifying slow-moving or obsolete inventory
For example, the Economic Order Quantity (EOQ) model uses a simple algorithm to determine the optimal order quantity that minimizes total inventory costs:
EOQ = sqrt((2 * D * S) / H)
Where:
D = Annual demand
S = Fixed cost per order
H = Annual holding cost per unit
More advanced algorithms can take into account additional factors such as lead times, seasonality, and product lifecycles to provide even more accurate inventory recommendations.
3. Route Optimization
In logistics and transportation, route optimization algorithms help companies reduce transportation costs, improve delivery times, and increase overall efficiency. These algorithms solve complex problems such as:
- Vehicle Routing Problem (VRP)
- Traveling Salesman Problem (TSP)
- Last-mile delivery optimization
One popular algorithm used in route optimization is the Clarke and Wright Savings Algorithm, which can be implemented as follows:
1. Calculate savings for all possible route combinations:
S[i,j] = d[0,i] + d[0,j] - d[i,j]
2. Sort savings in descending order
3. Starting from the highest saving:
a. If neither i nor j have been assigned to a route, create a new route (0, i, j, 0)
b. If i is already in a route and j is not, add j to i's route
c. If j is already in a route and i is not, add i to j's route
d. If both i and j are in routes, merge the routes if feasible
4. Repeat step 3 until all savings have been considered or all customers are assigned to routes
These algorithms can significantly reduce transportation costs and improve delivery performance, leading to increased customer satisfaction and operational efficiency.
4. Warehouse Management
Algorithms play a crucial role in optimizing warehouse operations, including:
- Slotting optimization
- Order picking strategies
- Labor allocation
- Automated storage and retrieval systems (AS/RS)
For example, a simple algorithm for determining the optimal picking path in a warehouse might look like this:
1. Sort items by aisle number
2. For each aisle:
a. If there are items to pick, enter the aisle
b. Pick items in order from front to back
c. Exit the aisle from the back if there are items in the next aisle, otherwise exit from the front
3. Return to the starting point
More advanced algorithms can take into account factors such as item popularity, weight, and size to further optimize warehouse operations and improve picking efficiency.
5. Supplier Selection and Evaluation
Algorithms can assist in the complex process of supplier selection and evaluation by:
- Analyzing supplier performance data
- Assessing risk factors
- Optimizing supplier portfolios
- Automating supplier scorecards
One common approach is the use of multi-criteria decision-making algorithms, such as the Analytic Hierarchy Process (AHP). The AHP algorithm can be summarized as follows:
1. Define the problem and determine the criteria
2. Structure the decision hierarchy
3. Construct pairwise comparison matrices
4. Calculate priority vectors
5. Check consistency
6. Obtain the overall priority ranking
By leveraging these algorithms, companies can make more informed decisions about their supplier relationships and reduce supply chain risks.
Implementing Algorithmic Solutions in Supply Chain Management
While the benefits of using algorithms in supply chain management are clear, implementing these solutions can be challenging. Here are some key considerations for successfully integrating algorithmic approaches into supply chain operations:
1. Data Quality and Availability
The effectiveness of algorithms heavily depends on the quality and availability of data. Companies need to ensure they have robust data collection and management systems in place. This may involve:
- Implementing IoT devices for real-time data collection
- Integrating data from multiple sources (e.g., ERP systems, CRM platforms, external market data)
- Establishing data governance policies to maintain data quality
- Investing in data cleansing and preprocessing tools
2. Choosing the Right Algorithms
With a wide range of algorithmic approaches available, it’s crucial to select the most appropriate ones for your specific supply chain challenges. This may involve:
- Conducting a thorough analysis of your supply chain processes and pain points
- Evaluating different algorithmic approaches based on their strengths and limitations
- Considering factors such as scalability, interpretability, and computational requirements
- Collaborating with data scientists and operations research experts to identify the best solutions
3. Integration with Existing Systems
To maximize the benefits of algorithmic solutions, they need to be seamlessly integrated with existing supply chain systems and processes. This may require:
- Developing APIs or middleware to connect algorithmic tools with legacy systems
- Updating business processes to incorporate algorithmic insights into decision-making
- Providing training to staff on how to interpret and act on algorithmic recommendations
- Implementing change management strategies to ensure smooth adoption
4. Continuous Monitoring and Improvement
The supply chain environment is constantly changing, and algorithms need to adapt to remain effective. Implement processes for:
- Regularly monitoring algorithm performance and accuracy
- Retraining models with new data to maintain relevance
- Conducting A/B tests to compare different algorithmic approaches
- Staying informed about new developments in algorithmic techniques and applying them when appropriate
Challenges and Considerations in Algorithmic Supply Chain Management
While algorithms offer significant benefits to supply chain management, there are also challenges and considerations to keep in mind:
1. Ethical Considerations
As algorithms play an increasingly important role in decision-making, it’s crucial to consider the ethical implications of their use. This includes:
- Ensuring fairness and avoiding bias in supplier selection algorithms
- Maintaining transparency in how algorithmic decisions are made
- Considering the impact of algorithmic decisions on employees and communities
- Adhering to data privacy regulations and ethical data use practices
2. Overreliance on Algorithms
While algorithms can provide valuable insights, it’s important not to rely on them exclusively. Human judgment and domain expertise remain crucial in supply chain management. Companies should:
- Encourage a balance between algorithmic insights and human expertise
- Provide training on how to interpret and question algorithmic recommendations
- Establish processes for human oversight of critical decisions
- Regularly review and validate algorithmic outputs
3. Handling Uncertainty and Disruptions
Supply chains are subject to various uncertainties and disruptions, from natural disasters to geopolitical events. Algorithms need to be designed to handle these situations effectively. This may involve:
- Incorporating risk assessment and scenario planning into algorithmic models
- Developing adaptive algorithms that can quickly adjust to changing conditions
- Implementing robust optimization techniques to handle uncertainty
- Regularly stress-testing algorithms under various disruption scenarios
4. Skill Gap and Training
Implementing and maintaining algorithmic solutions requires specialized skills that may not be readily available in many organizations. To address this challenge, companies should:
- Invest in training programs to upskill existing staff in data science and algorithmic thinking
- Collaborate with universities and research institutions to access cutting-edge expertise
- Consider partnerships with technology providers or consultancies to supplement in-house capabilities
- Foster a culture of continuous learning and innovation within the supply chain team
The Future of Algorithms in Supply Chain Management
As technology continues to advance, the role of algorithms in supply chain management is likely to become even more prominent. Some emerging trends and future directions include:
1. Artificial Intelligence and Machine Learning
AI and machine learning algorithms are becoming increasingly sophisticated, enabling more accurate predictions and complex decision-making. Future applications may include:
- Advanced demand sensing using deep learning techniques
- Autonomous supply chain planning and execution
- Real-time optimization of end-to-end supply chain operations
- Predictive maintenance for supply chain assets
2. Blockchain and Smart Contracts
Blockchain technology and smart contracts have the potential to revolutionize supply chain transparency and automation. Algorithmic applications in this area may include:
- Automated contract execution and payment processing
- Real-time tracking and verification of product origins and authenticity
- Decentralized supply chain coordination and optimization
- Enhanced traceability and recall management
3. Internet of Things (IoT) and Edge Computing
The proliferation of IoT devices and edge computing capabilities will enable more sophisticated real-time algorithmic decision-making. Future applications may include:
- Dynamic routing and scheduling based on real-time traffic and weather data
- Automated inventory management using smart shelves and RFID technology
- Predictive quality control using sensor data from manufacturing processes
- Energy optimization in warehouses and transportation
4. Quantum Computing
As quantum computing technology matures, it has the potential to solve complex supply chain optimization problems that are currently intractable. Potential applications include:
- Solving large-scale vehicle routing problems
- Optimizing global supply network design
- Enhancing cryptography for secure supply chain communications
- Improving financial risk modeling in supply chain finance
Conclusion
The role of algorithms in supply chain management is transformative, offering unprecedented opportunities for optimization, efficiency, and decision-making. From demand forecasting to route optimization and supplier selection, algorithms are helping companies navigate the complexities of modern supply chains with greater precision and agility.
However, successful implementation of algorithmic solutions requires careful consideration of data quality, integration challenges, and ethical implications. Companies must also strike a balance between leveraging algorithmic insights and maintaining human expertise and judgment in supply chain decision-making.
As we look to the future, emerging technologies such as AI, blockchain, IoT, and quantum computing promise to further enhance the capabilities of supply chain algorithms. Organizations that embrace these technologies and develop the necessary skills and infrastructure will be well-positioned to thrive in an increasingly competitive and dynamic business environment.
By harnessing the power of algorithms, supply chain managers can drive significant improvements in operational efficiency, customer satisfaction, and overall business performance. As the field continues to evolve, the integration of algorithmic approaches into supply chain management will undoubtedly become a key differentiator for successful companies in the years to come.